Validation System for Biometric Identification Chip
To take full advantage of a powerful eco-system
Abstract
For several years now, WireFlow has been helping a world-leading supplier of semiconductor chips for biometric identification in mobile devices, to set up, develop and maintain a validation platform for their products.
When developing ASICs for a mass market, it is vital that you have the capacity to validate the design of your product, without creating a bottleneck in your product development process.
Together with our client, WireFlow has created a platform with the ability to adapt and scale with the company’s innovations and short development cycles.
The Challenge
When a new ASIC is developed, its design must be validated on a number of pre-samples before it can go to mass production. The purpose of the validation is to make sure that the product shows the expected behavior and meets the defined requirements. Since market windows are narrow and delays are extremely costly, it is imperative that the validation platform is up for the task when the pre-samples arrive in the lab.
So, in short, our client needed a fast and reliable test system for both manual characterization as well as for automatic regression testing, to ensure that a new product meets with the requirements and can continue to mass production as quickly as possible.
The scope of the validation is to:
- Verify the correct functionality
- Characterize power consumption
- Check input and output voltage thresholds
- Check leakage currents
- Run continuity tests
- Run IDDQ test
Measure the quality of the AD converters- Test all modes, parameters, and functions
- Characterize the serial communication timing parameters like the setup-, hold- and valid times.
- Ensure that optimal settings are used for the highest possible sensor output quality.
Since our client uses external contractors for the production, they must be able to quickly assess the contractors’ production process as well as compare measurements with contractors’ production data.
When the client turned to WireFlow to get help to set up the new validation platform the following additional requirements where defined:
- One hardware platform to support all products.
- One software development tool to ensure homogeneous code.
- High degree of parametrization of platforms, with respect to test objects.
- Test-automation is a blessing
- Platform maintained by few, used by many.
- Increased and manageable traceability.
The Solution
Considering the requirements for performance, flexibility and, maintainability mentioned above, it was decided that we would go for a PXI-based hardware solution from National Instruments and use LabVIEW as the sole software development tool.
This would constitute a highly configurable hardware platform with a slot-in architecture which fulfilled the requirements we had at the time, but also give headroom for the future. It would also give us the possibility to utilize the highly integrated eco-system with drivers, applications and software development environment (LabVIEW), which National Instruments has created around their products.
About the hardware
The system we decided upon consists of the following components:
Controller PC
Standard PC with Windows 10 from HP with over-average, but not top-notch, performance.
NI PXIe-1073 chassis
PXIe-chassis with 5 slots. Connected to the controller PC
NI PXIe-6556/NI PXIe6570
Digital waveform generator/analyzer with PPMU capability. The PXIe-6570 replaced PXIe-6556 when it was suspended. Handles high-speed digital communication, analysis and, sourcing. Accurately measures small currents.
NI PXIe-6361: 16-bit high-speed analog data acquisition board
Handles timing and synchronization and can measure fast power consumption transients well.
NI PXIe-5152: 2-channel oscilloscope board Measures characteristics of the signals, such as amplitude, frequency, and rise time.
Adapter-board with Signal conditioning (customized design)
The built-in signal conditioning of the PXI modules is a big benefit since it reduces the amount of any required
Having all instruments in one, compact chassis instead of multiple separate
So … the software?
Eco-system, architecture & modular design.
All software we use are parts of the National Instruments eco-system, be it of-the-shelf-applications like the NI Digital Waveform Editor, configuration tools like NI-MAX, or LabVIEW, which we use to develop all test software and user applications.
The LabVIEW code that we have developed, is modular and carefully layered. By keeping to some simple rules when developing the code, we have been able to make the system 100% agnostic with regards to the DUT we connect to it. A big advantage since there is no setup time at all when switching between products in the system.
To introduce the newer PXIe-6570 as a replacement for PXIe-6556 in newer systems, was also a relatively easy task, and the software now runs transparently on systems regardless of which of the boards is used.
As mentioned, we have selected LabVIEW to be the sole software development tool. Everything, from
Sensor development support
Due to the modular design of the software, we have quite easily been able to develop user-friendly programs for other purposes than just formal design validation. One example would be “Tweaking-programs” that we create for the product developers when they want to explore new ideas for new functions in future products. We have also created programs to be used by support engineers when helping customers on-site.
Since the graphical LabVIEW code is very intuitive, we can communicate test code with sensor developers directly. Even though they are not LabVIEW programmers, they can read the code as flow-charts and get a grip on how we have implemented a test case and review the code to see if we are testing a certain function correctly. This has helped us speed up the test development cycles.
Production test support
A great benefit has been the possibility to use the digital waveform generator boards (6556/6570) together with the NI Digital Waveform Editor tool to create, edit and run test vectors on the PXI systems. This has enabled us to support the production test team in their work with the production tests.
For example, it is possible to:
- Review, evaluate and even create test vectors on our platform.
- Reproduce problems in our lab, that have been detected in a foundry by a contractor.
- Re-use test vectors developed by the production test-team in our validation test cases, which further decreases the time we need to implement them.
To conclude & looking ahead
The NI system delivers full coverage for both control and measurement, of all necessary inputs and outputs needed when testing the sensors. It is very reliable and can easily be scaled up in the future. It has met all our needs so far with wide margins, but we also have headroom in the system for future upgrades since we have a spare slot in the chassis.
And if even more slots will be needed in the future, it is possible to upgrade to a larger chassis with a relatively small effort.
The compact size and the modular design is convenient since we have been able to upgrade and add instruments in the system and we still have one single compact system, instead of ending up with more and more units on our desks.
The combination of LabVIEW and NI hardware empowered us to quickly get started with the system, and then let it evolve when the scope
The great success that the validation department has seen with a PXI-based solution has created an impact at other departments at the company. Not only the validation team has benefitted from the new platform, but so have for example the production test team, product developers and, others.
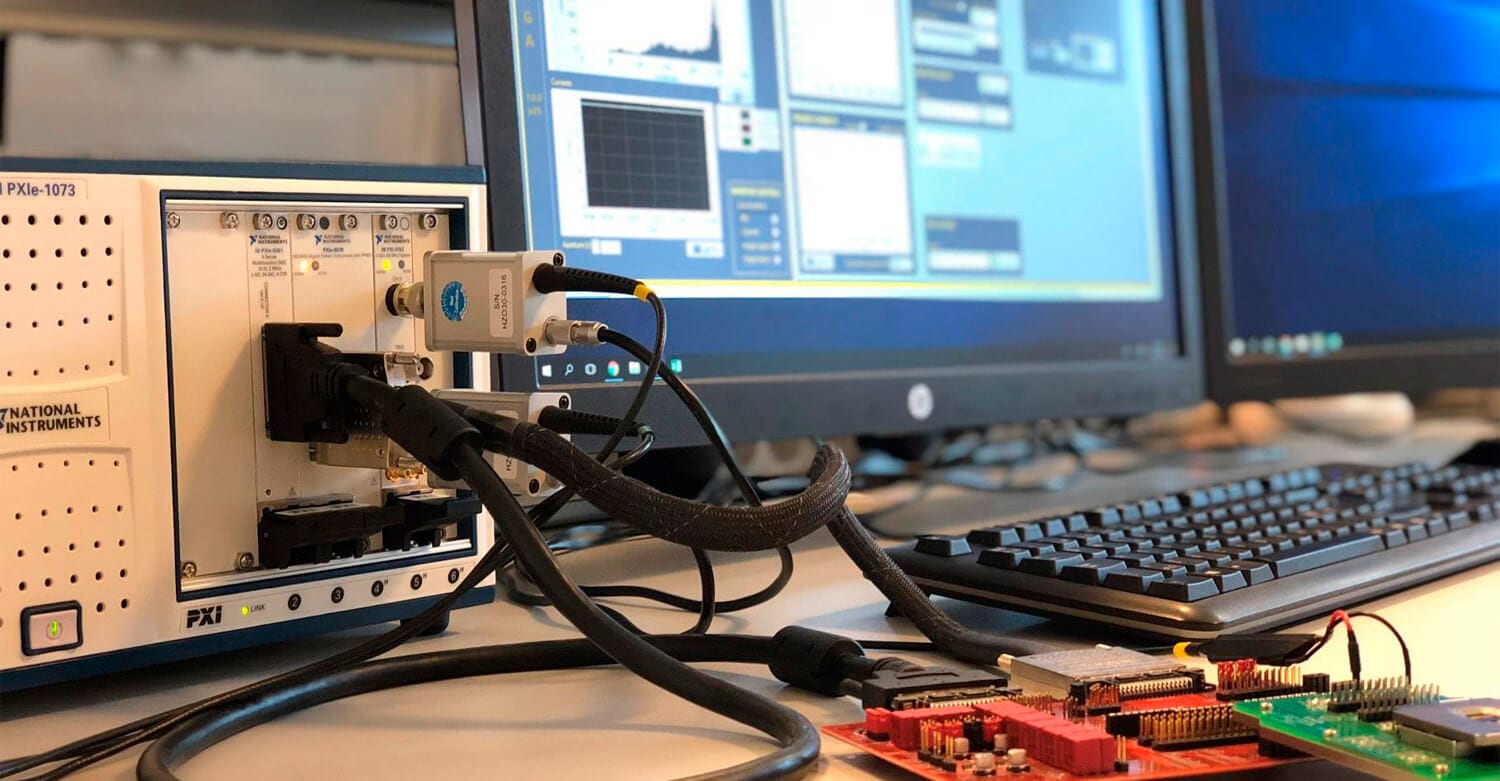
To conclude, we are happy to see that our client now has a modular, compact, scalable system with margins to handle future products. It is easy to duplicate and there is a very limited need for any customized electronics.